Una nuova collaborazione nel mondo Moto2
Come Deca Design ha collaborato con Boscoscuro e Team SpeedUp nella creazione di un telaio, utilizzando un metodo innovativo e originale.
CLIENTE
Luca Boscoscuro – Costruttore della moto, interlocutore diretto di Deca Design.
Team SpeedUp – Squadra di Moto2 che utilizzerà la moto con il telaio progettato da Deca Design.
OBIETTIVO
Virtualizzare il telaio e implementare le caratteristiche necessarie a raggiungere determinati target di risultato, innovando il componente con un nuovo metodo elaborato dal team di Deca Design.
SFIDE
Rendere attendibili le prove su pista anche nell’ambiente di simulazione, studiando il contributo di ogni singolo aspetto del telaio e degli altri componenti della moto. Il tutto sfidando le regole del ciclo “progettare – produrre – testare – scartare”.
IMPATTO
Ci troviamo nella fase finale di fabbricazione del telaio, e i test su pista inizieranno a febbraio-marzo 2024. Per tutto il resto… stay tuned.
Il cliente
In questo progetto il cliente è, per così dire, duplice.
Da una parte abbiamo Luca Boscoscuro, campione italiano ed europeo classe 250, ex pilota nel motomondiale della stessa classe e proprietario dell’azienda costruttrice di motociclette Boscoscuro s.r.l.; dall’altra il Team SpeedUp, il team di Moto2 nel quale corrono le moto di Boscoscuro.
Dopo averci conosciuto nel corso di un Gran Premio di Moto2 al quale i membri del team di Deca Design erano stati invitati, Luca Boscoscuro ha avuto modo di conoscere la nostra azienda in ogni suo aspetto, trovando in noi e nella nostra realtà tutte le qualità di cui aveva bisogno per la realizzazione di un telaio di nuova generazione, ad alto contenuto ingegneristico.
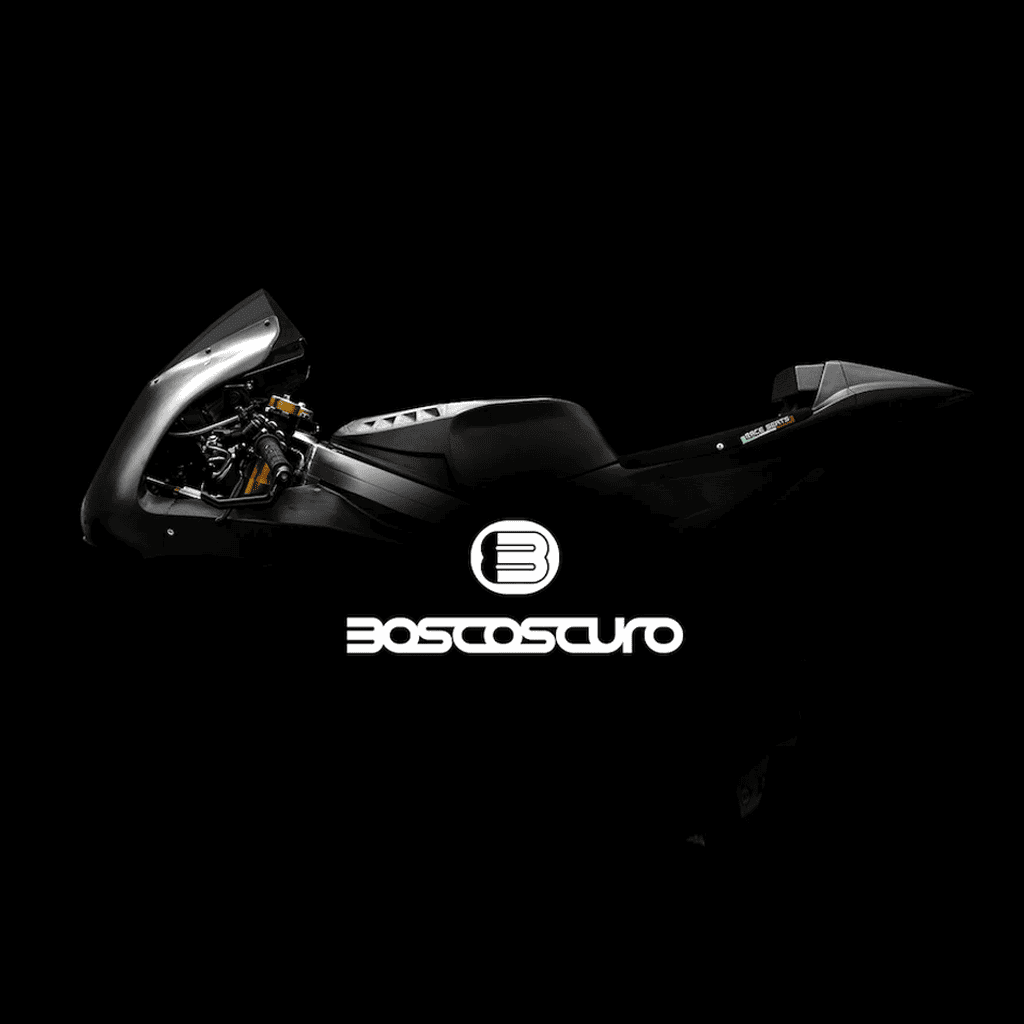
Gli obiettivi del progetto
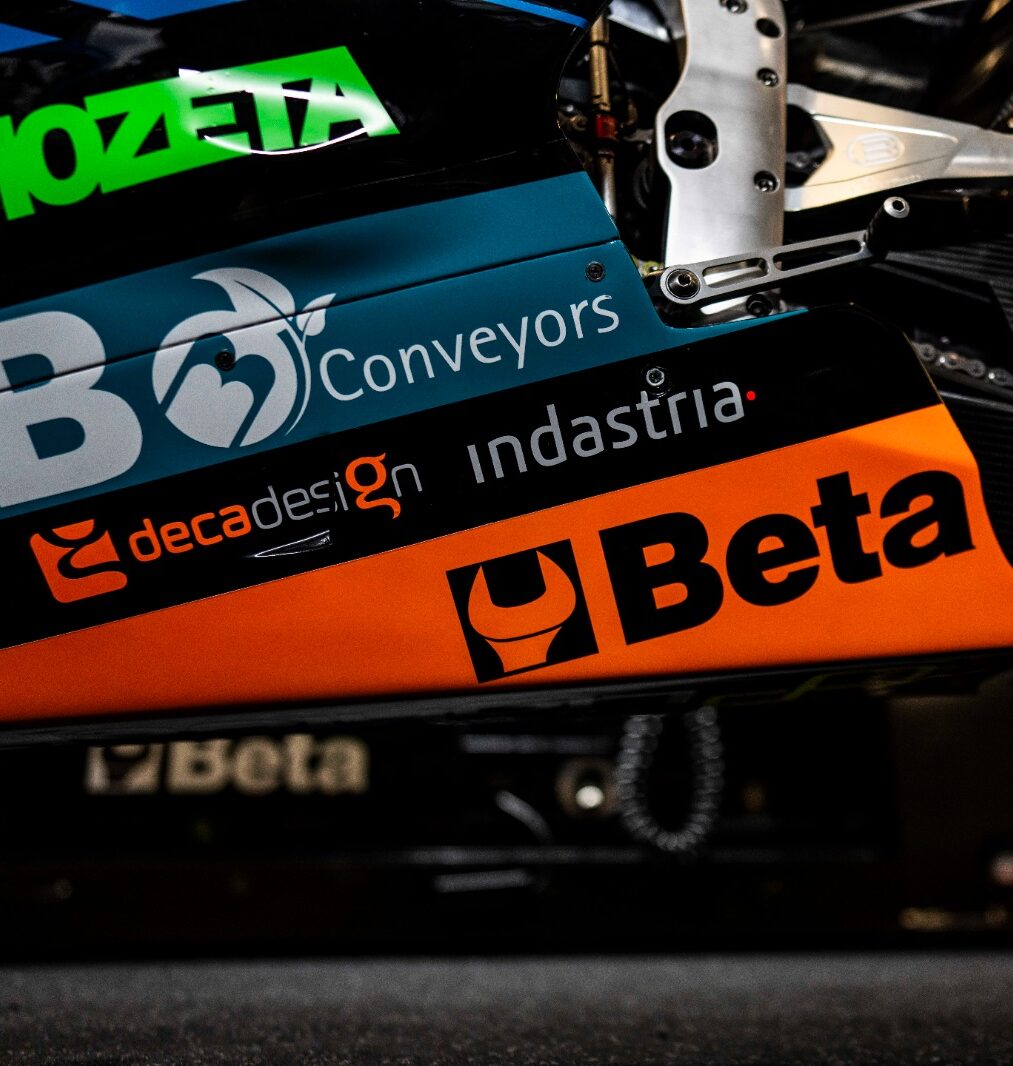
In Deca Design lavoriamo da sempre a schemi liberi, spesso senza avere a disposizione dei track record su ciò che realizziamo per i nostri clienti e partner: si tratta di un lavoro che è, si potrebbe dire, basato su un connubio tra “fantasia” e fondamenti di ingegneria.
Un approccio utilizzato anche per Boscoscuro: l’obiettivo principale della collaborazione ha infatti riguardato lo sviluppo di un nuovo telaio che, tenendo conto di specifici target di rigidezza, fosse capace di raggiungere le massime prestazioni in pista.
Per iniziare, abbiamo messo in campo un importante investimento in termini di rimodellazione del telaio: oltre a fare in modo che fosse conforme alle richieste del costruttore, abbiamo considerato ogni singolo ingombro e peso, poiché ogni grammo e millimetro in più e/o in meno possono fare la differenza in pista.
Il passo successivo ha riguardato la discretizzazione matematica e la creazione del modello di calcolo di riferimento; infine, una volta effettuate tutte le calibrazioni all’interno dell’ambiente virtuale, abbiamo potuto tarare il modello matematico secondo i target e le esigenze precedentemente indicati da Boscoscuro.
Le sfide affrontate
Dovendo lavorare in modo totalmente digitale, la prima sfida è stata quella di rendere attendibili anche nell’ambiente virtuale le prove che solitamente vengono effettuate al banco di prova telai e in pista; in altre parole, abbiamo costruito un modello matematico da zero, senza track record, combinando esperienza, fantasia e letteratura. Il tutto, ovviamente, doveva trovare riscontro anche nella realtà: in termini ingegneristici abbiamo lavorato alla discretizzazione della matematica pratica, rendendola virtuale.
A questa sfida si è aggiunta poi quella legata allo studio di tutti gli altri componenti, specialmente il motore, allo scopo di capirne il contributo sulla moto, sempre all’interno dell’ambiente virtuale: anche una variazione minima nel peso, nella forma o nelle dimensioni di questo componente potrebbe avere effetti di grande entità sulla moto nel suo complesso.
Il tutto si lega, infine, a un terza sfida: quella verso le regole del ciclo “progettare –
produrre – testare – scartare” tipiche negli ambiti in cui è veramente difficile fare una discretizzazione virtuale attendibile ed affidabile. Lavorare in un ambiente totalmente virtuale ci permette infatti di trasformare il ciclo utilizzato da molti costruttori, eliminando la parte di produzione “fisica” del componente e lasciano alle simulazioni digitali il lavoro di testing: ogni modifica necessaria viene effettuata, testata e valutata virtualmente, con un importante risparmio di tempo e di risorse.
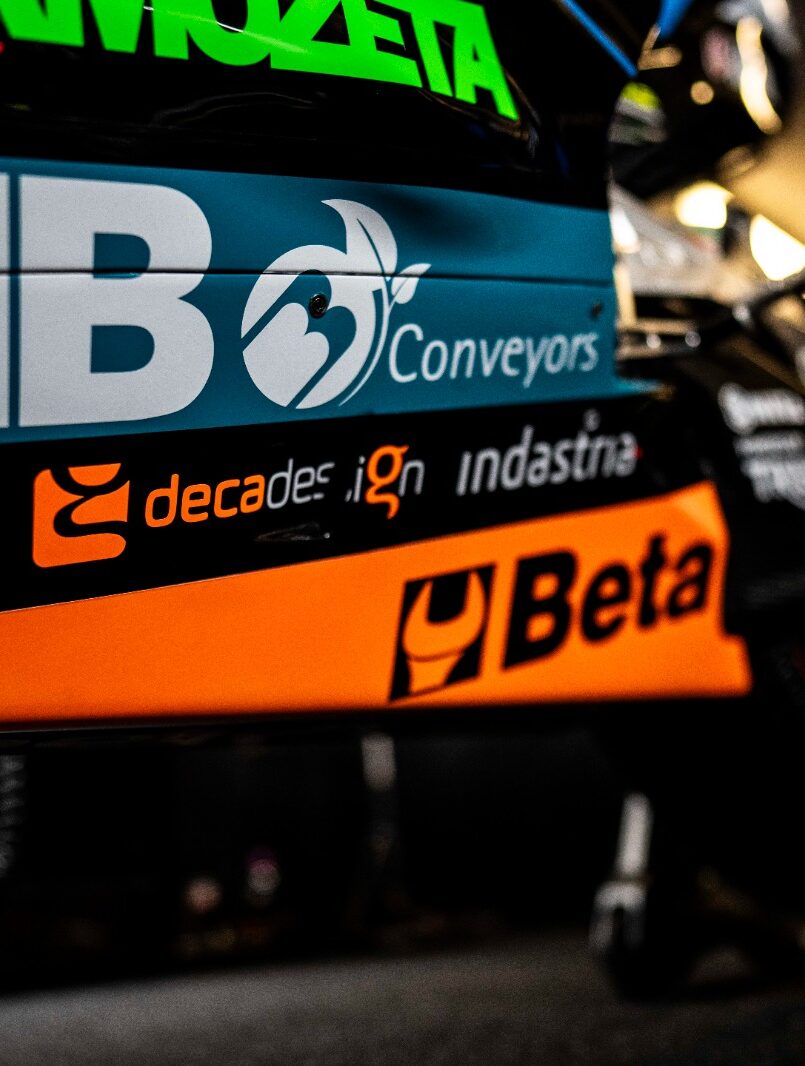